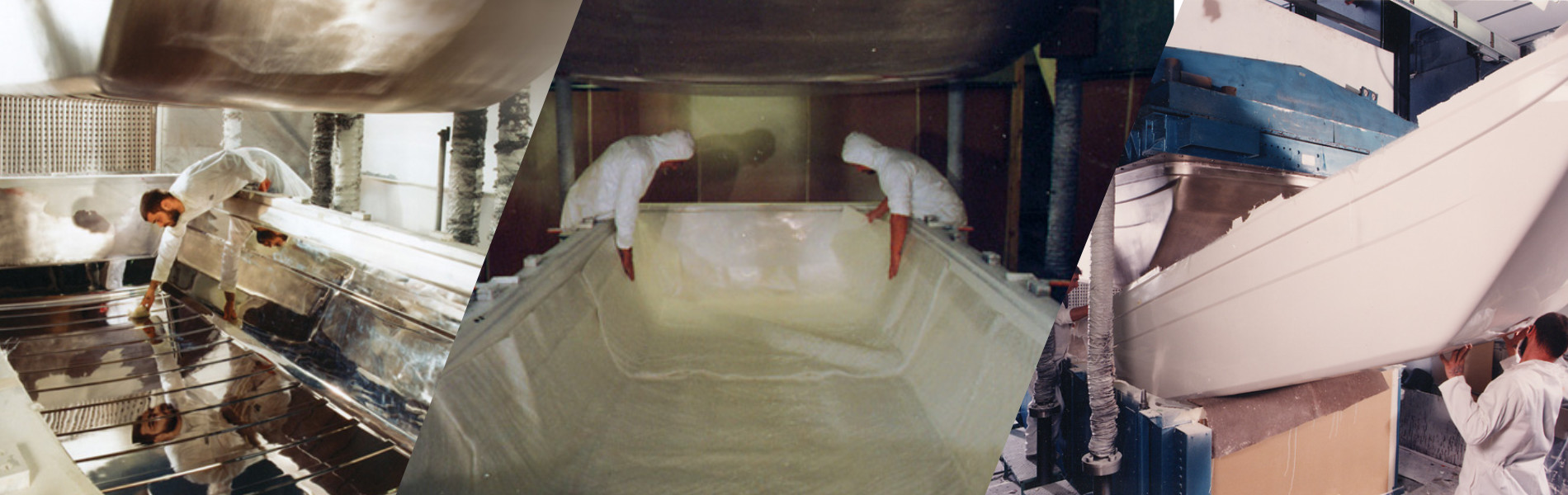
Wide range of FRP moulding techniques | Solutions for all sectors
We employ a number of moulding techniques including: Hand Layup, Spray Layup, LPPM (Low Pressure Press Moulding), RTM (Resin Transfer Moulding), RTML (Resin Transfer Moulding-Light), RI (Resin Infusion), and Polyurethane Low-Density Foam (foam cores for RTM, RTML, and LPPM).
Closed Mould moulding processes as listed above, i.e. LPPM, RTM, RTML, produce a smooth semi-cosmetic ‘B’ surface. Many of our customers prefer this, particularly where the end user will see the ‘B’ surface of the moulding.
By offering such a wide range of moulding techniques, we are able to provide the most appropriate solution, at a competitive price, in regular volumes ranging from a few to several thousand per year.
How do they work?
The five main moulding processes are similar in that they all produce a composite of a polymer matrix and glass fibres. Our most commonly used resin type is Polyester, and for particular applications, it can be formulated whilst in its liquid state to give specific properties, such as reduced shrinkage or flame retardancy. Phenolic or epoxy resins may also be used to achieve specific properties, such as low smoke emission or high strength composites.
During the moulding process, the resin is converted from a liquid into a solid polymer, encapsulating the glass fibres to form a composite structure. Most mouldings produced have a polyester gel coat surface, which may be high gloss, mat, or sand-able for paint preparation. Depending on geometry, gel coats can be textured to enhance the aesthetics of the moulding. Post moulding operations would include, trimming, drilling, assembly, and in some cases painting. Trimming and drilling may be either manual or robotic
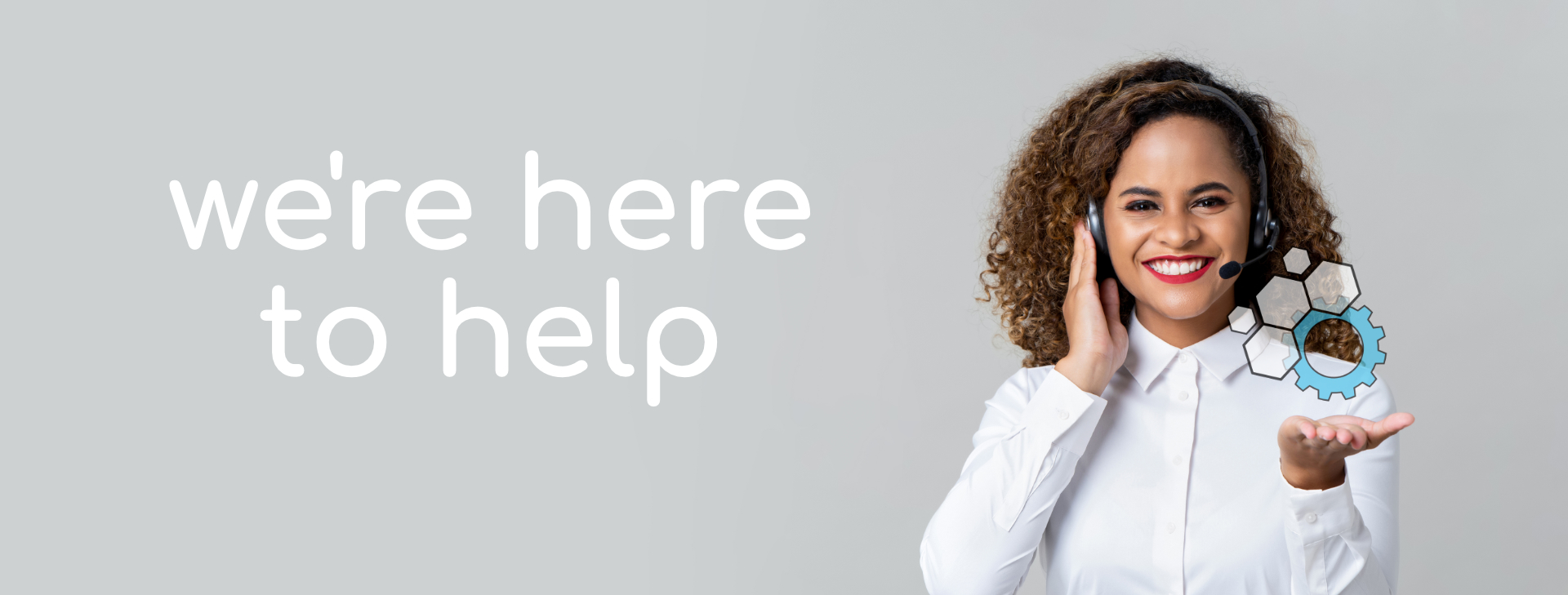
For further assitance, or for more information please contact us.